Explained: Fracking for Oil
- Uday Sirohi
- Jan 4, 2021
- 6 min read
Updated: Dec 30, 2021
The idea for fracking dates back to 1862 and has been credited to Edward A. L. Roberts. During the earlier days, explosives were used for shattering the surrounding rocks in the oil well but in the 1940s, explosives were replaced with high-pressure blasts of liquids, and so “hydraulic” fracking became the standard in the oil and gas industry. It wasn’t until the 21st century that fracking saw a massive boom and that was because of two innovations, first, the use of a certain type of fracturing fluid: slickwater, a mix of water, sand, and chemicals to make the fluid less viscous and second, horizontal drilling, a technique that increases the productive potential of each well.
What is Fracking?
Hydraulic fracturing, also commonly known as fracking, is a good stimulation technique involving the fracturing of bedrock formations by a pressurized liquid. It is a technique used for the extraction of natural gas or oil from shale and other forms of impermeable rock formations that lock in oil and gas and make fossil fuel production difficult. The process involves the high-pressure injection of 'fracking fluid' into a wellbore to create cracks in the deep-rock formations through which natural gas, petroleum, and brine will flow more freely. When the hydraulic pressure is removed from the well, small grains of hydraulic fracturing proppants (either sand or aluminum oxide) hold the fractures open.
How Does Fracking Work?
It involves blasting fluid deep below the earth’s surface to crack sedimentary rock formations—this includes shale, sandstone, limestone, and carbonite—to unlock natural gas and crude oil reserves.
Hydraulic fracturing requires an extensive amount of equipment which usually consists of a slurry blender to mix the fracking fluids, high pressure and high volume fracturing pumps such as triplex or quintuplex pumps, and monitoring equipment.

Source: US Patent No. 4390067A
Once a shale formation is targeted, an energy company will set up a drill pad, or home base, for drilling. The first step is to drill (with a drill bit typically 18-20 inches in diameter) vertically down past younger layers of rock that may surround a water table or contain younger types of gas. Once the hole is about 1,000 feet deep, a steel casing that’s thinner than the hole itself is inserted. Next cement is pumped down the casing, followed by high-pressure air, which pushes the cement to the bottom of the drill hole and up into the gap, or strings, between the steel casing and the surrounding rock. This becomes the vertical wellbore. The process is repeated until the drill hole is deep enough to reach the shale, which could be as deep as 10,000 feet below the surface, but typically caps out around 7,000-8,000 feet.
The invention of horizontal drill bits allows the wellbore to change direction once it is at a target depth. From a single drill pad, then, energy companies are able to drill multiple vertical wellbores within five feet of each other that are able to reach a very wide radius, sometimes miles wide, from the drill pad, thus eliminating the need to set up multiple drill pads across a landscape. The next step is to send small explosives or a perforation gun down to the targeted section of the horizontal wellbore to punch holes through the steel casing and cement. Once the holes are made, between 3 million and 5 million gallons of water containing a mix of sand and chemicals are pumped at extremely high pressure down into the wellbore. This fracking fluid explodes out of the holes, pulverizing the shale rock and creating multiple fractures or fissures throughout the formation. (FracFocus, a nonprofit website, keeps lists of chemicals used in fracking across the country, but disclosure is not legally required and companies listed submit their fracking solution “ingredients” voluntarily). The sand and chemicals of the fracking fluid sneak into the cracks created in the rock and hold them open, allowing for the trapped natural gas to flow back into the horizontal wellbore. The rock can be held open by just a few tiny grains of sand.
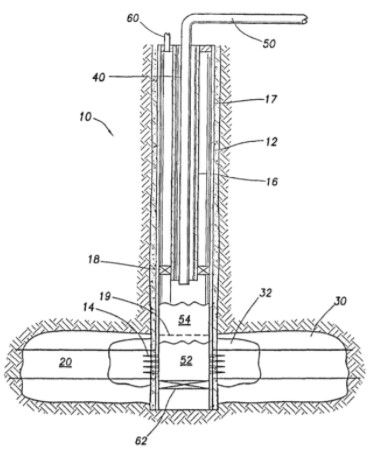
Source: US Patent No. 7569523B2
Associated equipment may include fracturing fluid tanks, proppant storage tanks, high-pressure treating iron, chemical additive unit, low-pressure flexible hoses, and various gauges and meters for flow rate, fluid density, and treating pressure. On the high end of the spectrum, the pressure used for hydraulic fracking may be as high as 15,000 psi and the injection rate could be as much as 100 barrels per minute.
The overall environment for fracking operations is very harsh, requiring equipment that can withstand extreme conditions. As hydraulic fracturing has become more widespread, the development of new and improved technologies has also ramped up.
Growing Demands
The demand for energy – and natural gas – has been increasing steadily. In 2019, the United States set a new record using 85.0 billion cubic feet per day of natural gas, up 3% from the previous year. From 2007 to 2016, annual U.S. oil production increased 75 percent, while natural gas production increased 39 percent, thanks to the advancements in horizontal drilling and fracking technology. In 2009, the American Petroleum Institute estimated that 45% of the United States’ natural gas production and 17% of oil production would be lost within 5 years without the usage of hydraulic fracturing.
Of US gas production in 2010, 26% came from tight sandstone reservoirs and 23% from shales, for a total of 49%. As production increased, there was less need for imports: in 2012, the US imported 32% less natural gas than it had in 2007. In 2013, the US Energy Information Administration projected that imports will continue to shrink and the US will become a net exporter of natural gas sometime around 2020.
Increased US oil production from hydraulically fractured tight oil wells was mostly responsible for the decrease in US oil imports since 2005. The US imported 52% of its oil in 2011, down from 65% in 2005. Hydraulically fractured wells in the Bakken, Eagle Ford, and other tight oil targets enabled US crude oil production to rise in September 2013 to the highest output since 1989.
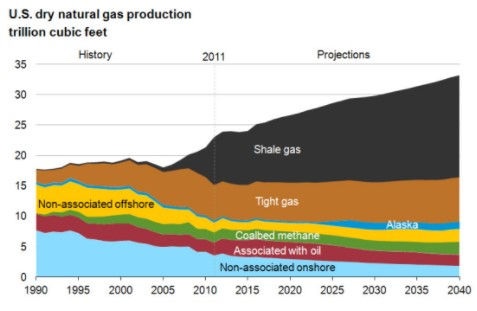
Source: U.S. Energy Information Administration, Annual Energy Outlook 2013 Early Release
Top Players
Halliburton (HAL) was the first company to carry out a fracturing operation back in 1949. Since then, they’ve been at the forefront of innovation and have now fractured over a million wells in the USA alone.
Schlumberger (SLB) is the largest oilfield services company in the world. It’s no wonder that they have a large pressure pumping section. Like Halliburton, they’ve been at the forefront of technological advancement. Through deals such as licensing agreements with Exxon Mobil (XOM), and acquisitions, they’ve stayed ahead of the pack. Just recently (Jan 2018), Schlumberger acquired Weatherford’s US fracturing assets for $430 million in cash.
Baker Hughes (BHI) is another big player in the hydraulic fracturing/pressure pumping space. They can also take credit for many of the technological advances in recent years. They run the Pressure Pumping Technology Center (PPTC) where their researchers focus on ways to frac more stages per day and reduce non-productive time (NPT).
FTS International (FTS) is lesser known than the first 3, but is one of the largest well completion companies in North America, specializing in fracturing. They have also entered into a joint venture with Sinopec in China to further their fracturing programs.
Together, these companies dominate around three-quarters of the fracking market in the USA.

The above graph shows a count of patent families the assignees have in the field related to Hydraulic Fracturing, and it can be seen that Schlumberger Technology, Halliburton Energy Services, and Baker Hughes are the three US companies that own most of the patent families.
As energy companies adopt technologies to equip themselves and their clients to take full advantage of the advanced technologies, they need to think about how to protect their native technologies and protect themselves against patent infringement lawsuits. Copperpod provides IP consulting services such as Infringement Claim Charts, Prior Art Search, Reverse Engineering and advises clients on patentability to give a clear picture of the state of the art to navigate away from the potential prior art and monetize IP assets.
References
http://www.eia.gov/energy_in_brief/article/about_shale_gas.cfm
http://www.bseec.org/technological_improvements_to_hydraulic_fracturing
https://en.wikipedia.org/wiki/Hydraulic_fracturing_in_the_United_States
https://drillers.com/pressure-pumping-which-are-the-biggest-fracking-companies/
https://www.worldsciencefestival.com/2014/08/frack-hydraulic-fracturing-101/
Uday is a research analyst at Copperpod IP. He has a bachelor's degree in Electronics and Communication Engineering. His interest areas are Microcontrollers, IoT, Semiconductors, and Memory Devices.
Comments